
If a sharper edge is needed, the tail of the anvil, or the portion of the long edges near the hardy hole, can be left more acute. Having used anvils now for significant time with very rounded edges of at least 3/8 inch radius, if not more, I find myself inclined to think that a significant pre-rounding of anvil edges is probably preferable and that working on an anvil with fairly large radii is rarely a problem. At the very least, a slight rounding of edges will help prevent this problem. I tried using it and it was leaving nicks all over everything I did. The face was milled perfectly and the edges were very square. My friend once imported a beautiful European anvil. A very square edge is both more fragile and can lead to deeper damage by chipping, and it can nick up your work and damage inside corners in bending.
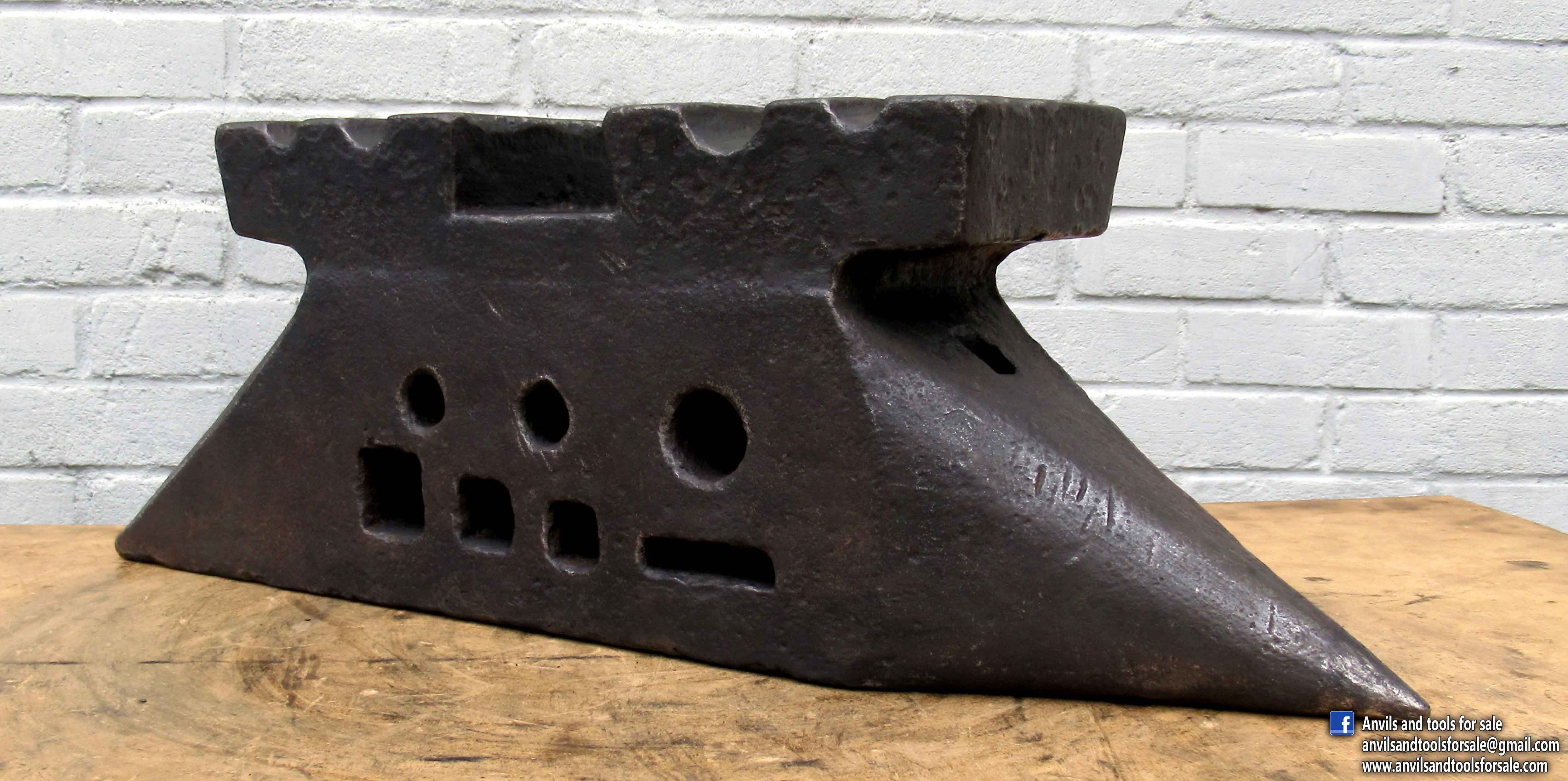
It may seem tempting to restore the anvil to it's original new condition, but a good argument can be made that the original square edges were more of a detriment than an advantage. Being someone who continually bounces their hammer off the anvil between blows, I have a great appreciation for anvil bounce. This hardness insures that the work surface remains flat and smooth. A good anvil will resist denting when doing cold work to some extent and will not easily be damaged by other tools, certainly not hammers, which are about the only other tools that should hit an anvil face regularly if reasonable care is exercised. Given this limitation in material performance, brittleness is the natural cost of having an anvil face that can withstand hard use. Tool steel is not bad at achieving both at once, but it still becomes more brittle the harder it is.
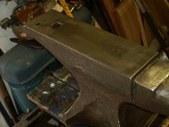

Most hard materials are also brittle to some extent. To find the two embodied to a high degree in any one material is a rarity. There is a difference between hardness and toughness.
